CRC 1153: Flexible process chain for the resource-efficient production of tailored forming components
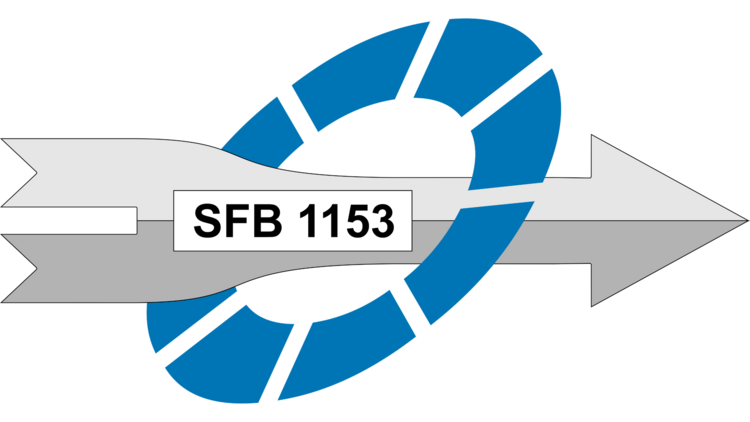
E-Mail: | blankemeyer@match.uni-hannover.de |
Team: | Sebastian Blankemeyer |
Year: | 2023 |
Funding: | DFG |
Within the framework of the Collaborative Research Centre (CRC) 1153, novel design, joining, forming, finishing and testing processes for the production of hybrid solid high-performance components were developed and realised in the first two funding periods. Within the third funding period, the individual processes in this sub-project will be linked to form an automated overall process in order to validate the functionality of the processes in a continuous process chain and to provide reproducible samples for the individual sub-projects. In addition to the mechanical structure of the system components, the controls must be networked with each other for a continuous process chain. In addition, a possibility must be created to record the process-relevant parameters by sensors and to store them in a component-specific manner in order to make data available to the sub-projects for the validation and optimisation of the individual processes, but also of the process chain.
By taking a holistic view of the process chain, the economic efficiency and resource efficiency are also to be investigated and increased. The economic efficiency of an automated forming process is highly dependent on the utilisation of by far the most expensive component, the forming machine, and its output. Compared to conventional forging, tailored forming technology currently has the disadvantage of long upstream semi-finished product production times in additional process steps, which leads to low output. For the decisive utilisation of the processes, the automated linking as well as their robustness is of decisive importance, since only in this way can economic production take place over larger batches. The methods to be developed will meet the challenge of long semi-finished product production times and the associated low utilisation while at the same time exploiting energy reutilisation potentials. In addition, the forming machine will be prepared for the parallel production of several components without retooling in order to avoid waiting times due to the different production times of the semi-finished products. The resulting new material flow in the process chain can be controlled variably and automatically according to the methods to be developed, so that the system always selects the ideal production process from the individual cycle times and process states. To reduce energy requirements within the tailored forming process chain, the targeted prioritisation of semi-finished products with a high temperature from the upstream process step makes the heat introduced usable for the subsequent forming.
For this purpose, a method must be implemented in production planning that takes various product and process parameters (e.g. cycle times, temperatures) into account when forming the sequence. The fully automated process chain also creates an opportunity to evaluate the industrial usability of the decentrally developed systems through endurance tests. The components produced in the process are used both for the validation of the overall process chain and for the individual processes.